And …. one day came up the Newood technology and suddenly my life changed. No skeleton, no framework anymore, no nailing, no bolts. Came up shell building. A double wooden shell perfectly maintained parallel by any wanted thickness of expanded polystyrene. All materials bonded 100% together. And with that material we produce prefab composite wood elements for general building. The prefab elements are bonded together with structural bonds of which the mechanical resistance is higher than those legendary of the wood fibers. A revolutionary, blow your mind, change your paradigm, building system.
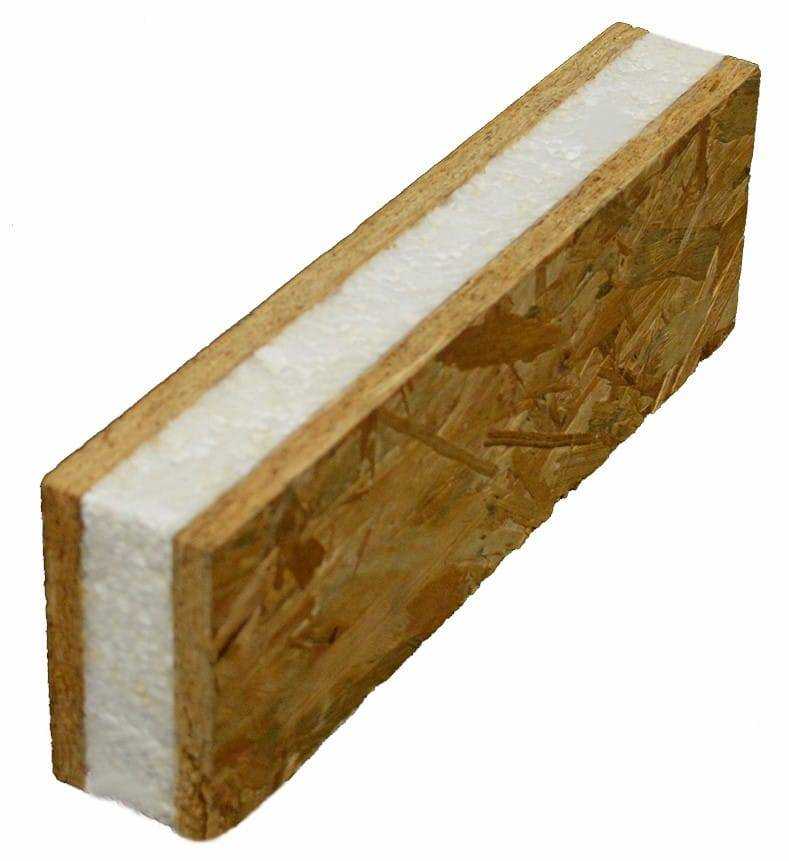
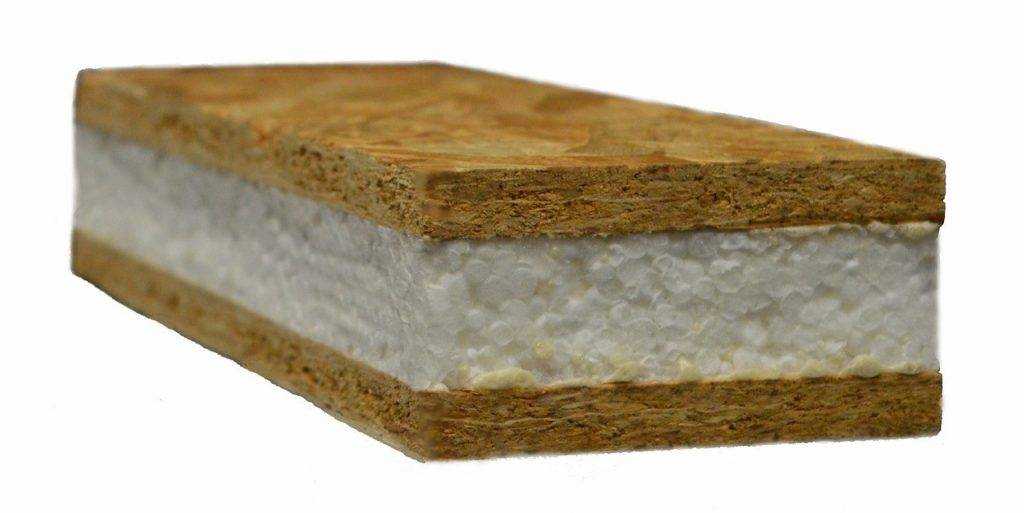
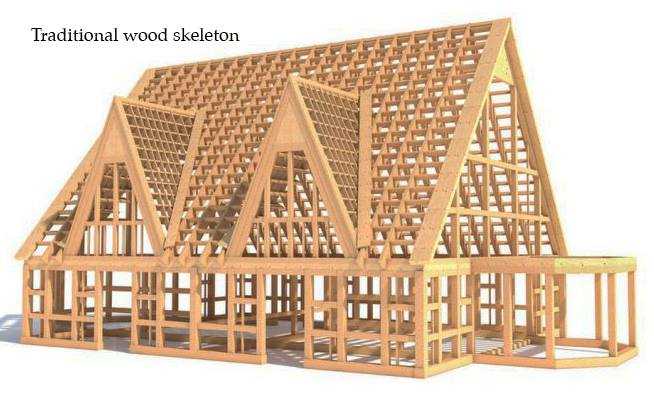
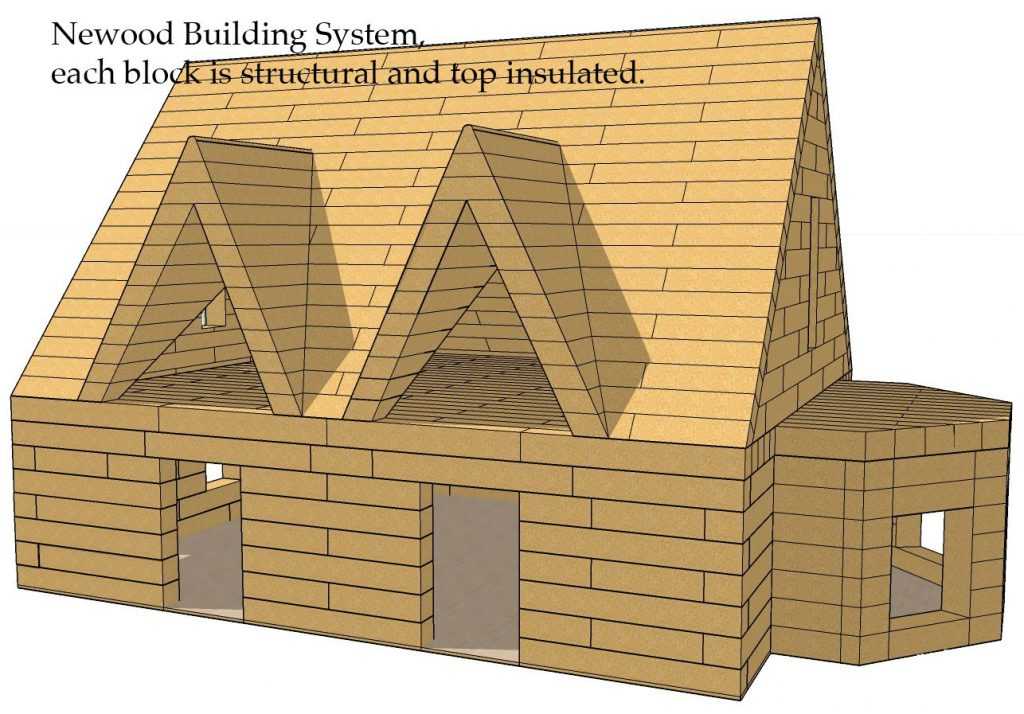
Traditional wood skeleton and Newood shell building compared.
I – Newood, the building material.
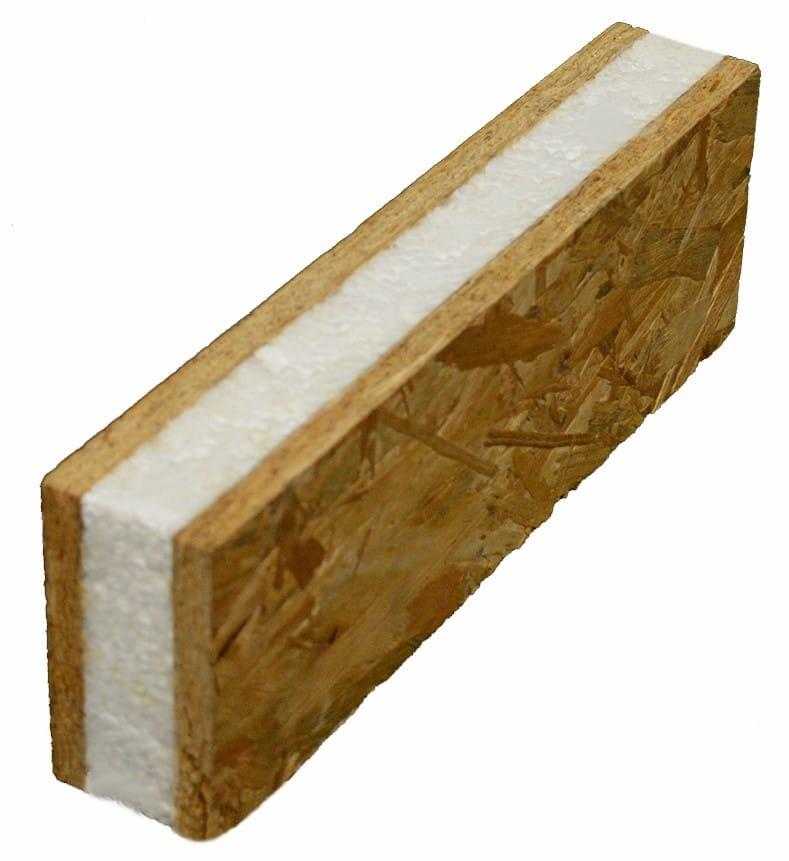
Newood is first of all a composite building material that belongs to the wood industry. The assembly of high quality expanded polystyrene and OSB wood panels with structural adhesives makes it possible to obtain what is called a sandwich material (in physics «the sandwich effect»). With this assembly we realize blocks whose standard one is 2m50 long by 40 cm high and 40 cm wide. The width of the blocks (40 cm) determines the thickness of the walls, floors and roofs. The blocks are sized to allow for all constructive shapes: flat, curved, double curved and spherical.
II – Newood, the hidden dimension.
In the thickness of the blocks, we can operate and circulate. From now on the exterior and interior doors will be pocket doors. Not a sliding door fixed on a wall, but sliding in its thickness. Likewise, for insulated pocket shutters (also highly break-in resistant).
In terms of circulation, we offer ducts for electricity, water, telephone and other AI systems. At the centre of our blocks we introduce at the request of architects and thermal engineers ventilation tubes for the transport of fresh air from geothermal origin (horizontal and shallow).
III – Newood, the building system.
The blocks necessary for a construction are bonded together with structural bonds. These bonds have tearing and shearing resistances far superior to those of the legendary wood fibres. Once the blocks are bonded together, we practise an exterior and interior reinforcement of all walls, floors and roofs (double-sided) with OSB panels by bonding with structural bonds. What we call the inner and outer reinforcement by lamination (in physics the lamination effect). With the Newood technology, we don’t nail or screw anymore.
Newood constructions are particularly homogeneous. From the first row of the ground floor to the ridge, the same material runs everywhere. By the conjugated sandwich and lamination effects we obtain constructions with «a high and favourable ratio of strength/weight» (J. Conte, Professor in structural engineering and earthquake design at the UCSD and director of the NHERI shake table).
With a thickness of nearly 40 cm of EPS insulating foam, Newood constructions are a-thermal. Outdoor temperatures (cold or hot) cannot penetrate a Newood building. This allows the Newood technology to ensure a top worldwide insulation level. Thanks to the integrated ventilation system, the Newood constructions offer a real air conditioning. In winter or summer, in all latitudes, they can provide 20°C inside.
The bonding of block elements creates a perfect distribution of internal loads of walls, floors and roofs. By bonding the Newood structures on a concrete floor slab, the load lowering is distributed over the entire circumference unlike the wood frame construction where it is concentrated only on the feet of the skeletons.
IV – Newood, earthquake, hurricanes and tornadoes resistant.
It is the constructive homogeneity that makes Newood, yet a lightweight material, so resistant. In exceptional circumstances, constructive elements cannot de-solidarize. We can turn over a Newood construction as a ship without the slightest collapse. The hurricanes and tornadoes clearly show the «disassembly» due to the lack of constructive homogeneity of traditional technologies. One tile, a piece of sheet metal or a roof overflow that let go and in seconds a construction can be destroyed. On Newood constructions, winds can’t find grips.
V – Newood, the main metrics.
In summary, the key metrics of the Newood technology are:
– the very high mechanical strength,
– the a-thermal insulation (habitats that no longer require heating),
– the exceptional formability (a new dimension for architects), and
– the building costs of 20 to 30% lower than existing technologies.
With Newood, no heating, no damage, no death toll, no fatality.
——————————————————————————————————————–
About Expanded Polystyrene.
The chemical formula of expanded polystyrene is : (C8H8)n. It is purely carbon and water. There are no other molecules in expanded polystyrene (EPS).
It is made from styrene from petro chemistry. When refining crude oil, it is first extracted kerosene, then gasoline, diesel and domestic fuel. This leaves the tar from which the styrene is extracted, which could have been extracted from other resources such as coal and even possibly wood. Styrene is an oil by-product.
The styrene is then transformed into balls that, in contact with water vapour and butane or pentane gas, will expand in a mould to the desired form and contain no ozone-depleting gases. The EPS industry has an excellent professional reputation. It is a clean industry, by no means dangerous, never stories, no alarming articles in the press, good reputation, etc. The production of EPS is still a sophisticated technology with highly skilled technicians. The EPS can be completely recycled !
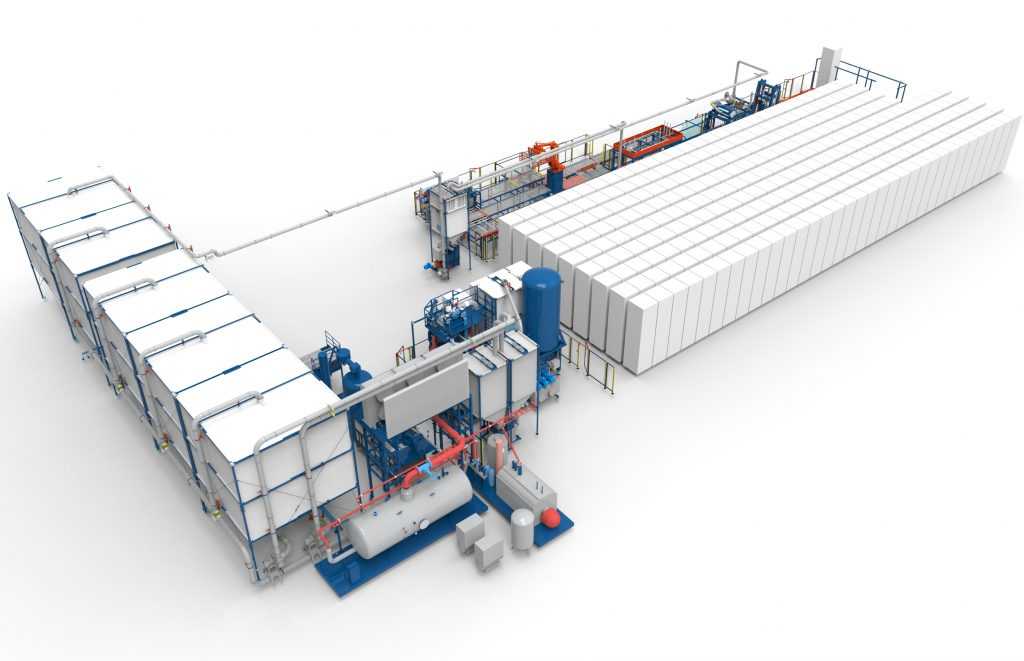
Originally, after the Second World War, the EPS was designed for housing insulation. A few years later, the packaging industry discovered the excellence of the EPS for the protection in particular of fragile objects (good maintenance, protection). This resulted in buyers of appliances and other televisions or computers rushing to throw out EPS packaging as if it were the most vulgar material just good for the trash. Followed by insulating cups and other food trays (daily).
The EPS has defects, but also some well concealed qualities that make it a material unlike vulgar, very noble.
EPS is brittle, poorly resistant to UV and solvents. It is flammable like wood (carbon).
The EPS hides a formidable constructive shear resistance and without UV or presence of solvents, well wrapped by wood it is very resistant to aging.
The EPS can be moulded with very high precision, it is also dimensional-ly very stable.
EPS is non-toxic. As evidence, it is used extensively for packaging foods such as meat and fish. Who didn’t buy their steak in a tray at the supermarket? EPS cups are used daily by crowds of beverage consumers.
Regardless of what competitors want to say, EPS is currently the best known insulator. What architecture schools teach in France and elsewhere. The only way to build a-thermal habitat! Is it necessary to recall that one-third of the national energy bill is used for home heating?
Contrary to what some say, the production of EPS does not require much energy. The necessary energy is used exclusively for the production of steam and for cutting into plates or blocks.
The EPS is cheap. A cubic metre of 18k/m3 EPS costs nearly 90 euros/m3 rendered. Compared to the price of OSB panels that cost 500 euros/m3 and that requires much more energy (cut down the trees, grinding and hot pressing in colossal presses). And because OSB panels are made of wood they would be greener than EPS(carbon)? EPS is produced strictly to Iso and Din standards.
On the Internet there are people who like to convey fake information. That EPS is not biodegradable. That it takes 500 year (!) for the soil to digest. And where does this delay come from? Accelerated ageing tests in a laboratory. What is incomparable with aging in the earth, where sand and gravel will rub and grind it, as well as insects and other micro-organisms that will accelerate aging.
In the field of general construction, the sustainability of buildings is now often discussed. Modern constructions do not age well, do not last long enough. Individual habitat has difficulty surpassing the fifty-year mark without often, deep renovations. Can we then blame polystyrene for being durable? Certainly not.The danger of EPS is of another order, human neglect. Our own neglect that hurts birds and even more fish. Birds can take EPSbeads for seeds and possibly suffer from an indigestion. In no case will they settle on a piece of EPSto rip out marbles to feed themselves. The worst is for fish. EPSbeads are translucent and when ingesting plankton or small prey, a fish can swallow them sustainably without noticing and block its digestion system in a lethal way. You all know where these EPS beads come from and why they end up in the sea.
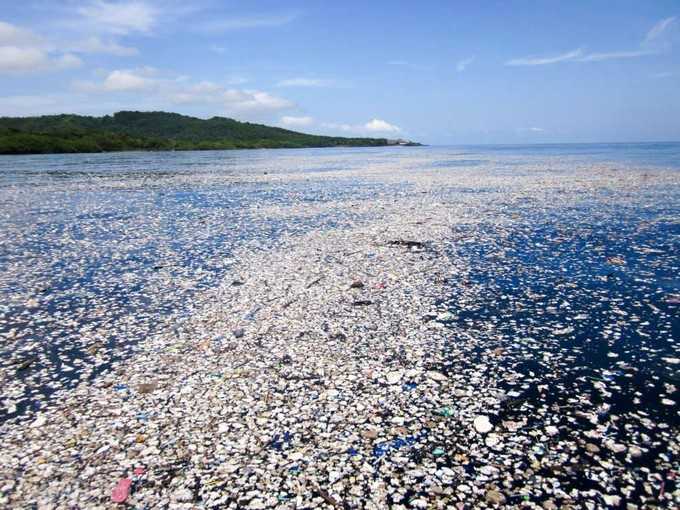
By our cumulative individual negligence.
The EPS has, wrongly, an undeserved bad reputation. It is a perfect, durable and mechanically excellent insulator to produce a sandwich or composite type building material. Provided it doesn’t hang around. The EPS in the sea does not come from general building, but from packaging. Good hearers, hello. Willem.